You have no items in your shopping cart.
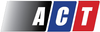
0item(s)
You have no items in your shopping cart.
Introduction
Powder coating operations are among the leading modern finishing techniques: offering durability, corrosion resistance, and aesthetic appeal to coated products. Central to the success of any powder coating process is a rigorous quality control regimen, and one essential component in this regimen is the use of test panels. The right test panel and process can help save a coater money, gain business, and trouble shoot concerns.
Examples of test panels in various configurations
The Fundamental Role of Test Panels
Test panels function as surrogate substrates mimicking the properties of the products intended for coating. If coated alongside actual products in the powder coating line, these panels allow for a direct and controlled comparison of finish quality and performance. This comparative analysis not only highlights potential issues in the coating process, but also enables fine-tuning for optimal results.
The Panels
A quality finishing operation centers on visual and durable attributes. Substrate, surface treatment, paint application, and curing all play a role in producing quality painted parts. Multiple types of test panels should be deployed to provide the best results and make QC cost effective. The different panels to deploy include:
Bare utility panels – Inexpensive base metals that are clean and ready for coating.
Controlled substrate panels – Designed to take the “noise” out of quality testing that focuses on pre-paint and surface treatment processes. These panels require preparation before coating and must be from a consistent and traceable supply.
Controlled surface treated panels – Panels produced in a controlled environment with a prepared surface treatment for benchmark testing. They should have a similar, or slightly superior, quality, to the surface treatment that is tested.
The Usages of Panels
Calibration and Benchmarking
Before initiating any coating job, it's essential to calibrate your coating equipment and establish a baseline using test panels. This involves setting the equipment to the desired specifications: coating thickness, temperature, and cure time. The test panels serve as a reference point for ensuring that your equipment is operating correctly.
Visual Inspection
While a simple process, visual inspection of test panels is an effective method for evaluating the coating's appearance and finish. Examine test panels for defects like orange peel, pinholes, craters, or color discrepancies. Identifying issues on test panels allows you to address them before they affect production parts.
Color Matching
Color consistency is vital in many powder coating applications, especially in industries like automotive and consumer electronics. Test panels can be used for color verification and ensuring that the coating's color is consistent across all parts.
Monitoring Coating Thickness
Coating thickness is a critical factor in powder coating quality. Specialized gauges, such as magnetic or eddy current gauges, measure thickness. Regular measurement of coating thickness on test panels ensures consistent compliance with quality standards.
Adhesion Testing
Adhesion is another key aspect of powder coating quality. Test panels are subjected to cross- cut or pull- off adhesion tests. These tests assess the bond strength between the coating and the substrate. Proper adhesion ensures the coating won't chip, peel, or flake prematurely.
Salt Spray Testing
Salt spray testing simulates harsh environmental conditions to evaluate the coating's ability to withstand corrosion. By subjecting test panels to salt spray tests, you can assess the durability of the coating.
Impact and Flexibility Testing
Depending on the application, some parts may need to withstand impacts or flexing- without damaging the coating. Test panels provide a sacrificial surface to help evaluate a coating’s resilience under those stressors.
Chemical Resistance
Proper testing on panels ensures that the coating won't degrade or react negatively when exposed to chemicals or solvents.
Any successful powder coating process includes using test panels. A good test panel saves a coater money, promotes business, and trouble shoots concerns.
Scott Crosley is a 28 year veteran in the paint and coatings industry. After a long career at Sherwin Williams, Scott currently serves as the Vice President – Business Development & Sales at ACT Test Panels.
← Older Post
0 comments