You have no items in your shopping cart.
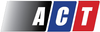
0item(s)
You have no items in your shopping cart.
Introduction
Zinc phosphate is commonly used on aluminum surfaces. It is a chemical conversion coating that provides corrosion resistance and improves the adhesion of paint or other coatings. When sparse zinc phosphate occurs, the surface will shine through the normal matte appearance. This is a quick indication that coating is incomplete.
Any contaminants on the aluminum surface, like oil, grease, or dirt, can interfere with the formation of the zinc phosphate coating. Properly clean the surface before applying the coating.
Aluminum surfaces need to be properly activated before coating. This typically involves an acidic solution or etching process that fosters adhesion.
Most people talk about coating weight as it relates to the quality of pretreatments. With zinc phosphates, it is also important to look at the coverage and crystal morphology of the coating. With a microscope, it is easy to see and confirm that the shiny areas are voids in the treatment- beyond voids, it is a good practice to look at the structure and size of the surface crystals. Spray will be block like and jagged, immersion will be smaller and round. Without consistent coverage, even if coating weight is achieved, corrosion control will be compromised.
Fluoride
Fluoride plays a limited but specific role in zinc phosphate coatings. While not always included, it can offer certain benefits, certainly when processing aluminum:
Etching and Activation:
In low concentrations, fluoride ions can slightly etch the zinc surface, promoting the growth of the phosphate layer. This can be particularly beneficial for aluminum substrates before applying a zinc phosphate coating, as it improves the coating's uniformity and development.
Crystallization Control:
In zinc phosphate processes with specific additives, like hydroxylamine, fluoride ions can help control the crystallization of the phosphate layer. This allows for the formation of a finer-grained and denser coating, which can improve corrosion resistance.
Efficiency Improvement:
In rare cases, specifically for aluminum, adding low levels of fluoride along with iron ions can improve the efficiency of the zinc phosphate conversion process. This can result in better coating weight, reduced sludge formation, and improved appearance of the final coating.
Excessive fluoride can be detrimental. It can dissolve the forming phosphate layer- leading to a weaker and less effective coating.
Therefore, the use of fluoride in zinc phosphate coatings is not always necessary and should be carefully evaluated based on the specific process, substrate material, and desired outcome.
Conclusion
If the coating is too thin, it may not provide sufficient corrosion resistance or adhesion. Use a suitable application method, such as spraying or immersion, to achieve the desired thickness. Thoroughly cleaning the surface, properly activating it, and ensuring adequate coating will yield a durable and even finish.
Scott Crosley is a 28 year veteran in the paint and coatings industry. After a long career at Sherwin Williams, Scott currently serves as the Vice President – Business Development & Sales at ACT Test Panels.
← Older Post Newer Post →
0 comments